“Lean manufacturing is a fundamental part of our business,” begins David Davis, Operations Director at Trovex. “This means putting the right processes in place to maintain quality, accuracy and speed of fabrication.” To assist in this manufacturing process, the hygienic interiors manufacturer has invested in its first Striebig Control 4216 vertical panel saw, which was supplied and installed by machinery distributor, TM Machinery.
As well as hygienic wall cladding, wash stations and cubicle systems, the Welham Green-based manufacturer also produces PVC encapsulated doors for the commercial sector. With production of its high-end door sets almost doubling in the last 12 months, David and his team were keen to invest in a new machine that could maximise efficiency and offer unswerving precision, speed and reliability in the face of increasing orders. “We were previously cutting chipboard door blanks and birch ply or MDF internal door linings on a sliding table saw,” explains David. “Handling was difficult, with panel sizes measuring up to 3m x 1220mm and door blanks measuring 900mm x 2.2m. Without a digital control, we also had to rely on the precision of individual fabricators.
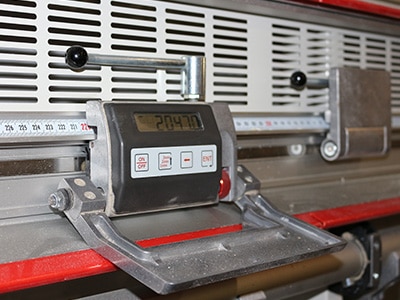
“Unlike a conventional door, that can be planed on-site to fit, our doors are fully encapsulated and are therefore manufactured to fine tolerance. This means every door that leaves our factory must fit the frame perfectly to avoid costly adjustments and delays. This made accuracy one of the most important factors to consider when specifying a new cutting machine.”
Striebig Control 4216
With the addition of a grooving unit, the laser-assisted Striebig Control 4216 vertical panel saw, equipped with digital measuring system on both axes, programmable control system and automated cut cycle, ticked all the boxes for Trovex and has helped the company develop its lean manufacturing programme. “As soon as we saw the Striebig in action, there was no hesitation in my mind that this was the ideal vertical panel saw for us. The Swiss brand has a great reputation and, with TM Machinery’s knowledge of the machine, we had every confidence in them and the saw’s abilities,” says David. “We were not disappointed and we saw results immediately. The whole process has been simplified and cutting is always accurate thanks to the saw’s automated functions. What was previously a two-man operation is now the responsibility of one fabricator, and the time it takes to cut materials to size both vertically and horizontally has been slashed.”
Striebig Increasing Efficiency
The saw has already played a key role in several projects commissioned by the health authorities. “We had a very challenging installation at a London hospital at the end of last year that would have taken considerably more time without the Striebig,” says David. “We needed to replace the existing door frames on a live hospital ward but they were made from steel and filled with concrete. To remove them would have involved a lot of time, dust and noise, so we came up with a system that essentially allowed us to fit a door within a door, cladding the existing door frames in the process. The concept needed complete accuracy to limit disruption on the hospital ward. The Striebig was invaluable in this installation and allowed us to complete the project with minimal fuss and within a shorter timeframe.”
David adds, “The Striebig has already brought a lot of benefits to the business and we’re now in a position to work on a wider range of projects. Research and development is high on our agenda and we’re always looking at ways to improve what we do. The introduction of the ‘Control’ has given us the opportunity to innovate and maximise our potential, whilst maintain our core manufacturing processes.”
For more information on the complete woodworking machinery range offered by TM Machinery Sales Ltd. and its servicing division, TM Services & Spares Ltd., call us on 0116 271 7155 or fill in our contact form.