New Striebig Compact Wall Saw
Following the successful buy-out of a local competitor in December of 2018, custom-built exhibition stand designer and manufacturer, GH Display, is predicting its most successful year yet, as project work hits a record high. Consistently growing 30% year on year since 2013, the Peterborough-based, family-run company is on course to quadruple its weekly production rates in 2020 thanks to ongoing investment in its workforce and the installation of a new Striebig Compact wall saw.
“We pride ourselves on offering a complete service package,” begins John Hodson, Managing Director of GH Display. “We not only design and custom-build each component in-house, we also pre-assemble the entire exhibition stand in our workshop before transporting it to its location and building it again on-site to guarantee the very best results. It’s a military operation and if one part of the operation fails or holds us up in some way, it can easily lead to a domino effect. That’s why, when our old saw started to show signs of slowing down, we knew it was time to invest in a new wallsaw.”
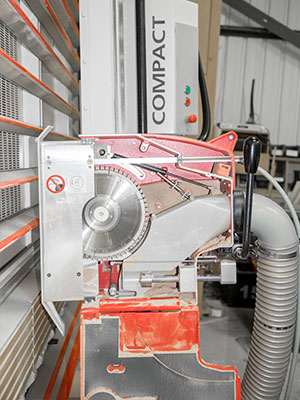
The company’s old sawing machine was bought in 1995 and had served the company well but, following a move to new premises in 2018 and an increasing workload, the panel saw couldn’t keep up with demand. “I didn’t want this to have a negative impact on our production, so I began researching vertical panel saw manufacturers,” explains John. “I was taken aback by just how far these machines had come on since I was last in the market for one. To make a sound decision, I wanted to work with a company that could offer me honest advice and technical know-how. It was through a recommendation that I started to look into Striebig wallsaws and talk to their UK distributor, TM Machinery. I looked at several models with TM Machinery’s specialists and we spoke in detail about our company, our requirements and each machine’s capabilities. It was clear that the Striebig Compact panel saw was the right wallsaw for us and six weeks later, it was installed in our workshop by a Striebig engineer.”
The use of MDF, Plywood, Laminate and Foamex
As well as cutting standard MDF and Plywood panels ranging from 4-15mm in thickness and a small number of laminate sheets, one of John’s requirements was that his new vertical panel saw needed to cut 1.5m Foamex PVC board with a 1-10mm thickness.
“Our old saw couldn’t accommodate large Foamex sheets, which led us to manually cut the sheets down using a jigsaw to fit the saw,” explains John. “This process took time and could have easily led to mistakes being made. Now, with the Compact, we have the option of a 1.5 cut height, which gives us the flexibility to work easily with larger sheets, saving us time and reducing material wastage caused by inaccurate cuts. Its support rollers and easy-to-use measuring system have also helped to simplify this process.”
A wall saw designed to last
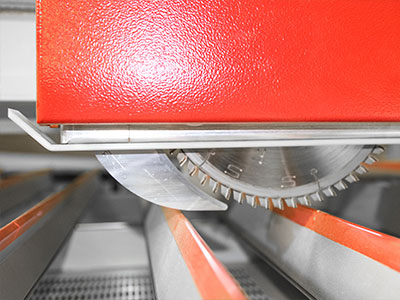
Future-proofing was also a key area of consideration for John and something TM Machinery was keen to pinpoint during the sales process. “Our increased production was certainly an important factor for all parties involved. We were cutting around 120 sheets of MDF and 40 sheets of Plywood per month but this number keeps increasing. The panel saw needed to cope with increased production, whilst also maintaining high levels of accuracy and a high quality finish for the foreseeable future.
“The Striebig Compact panel saw has not disappointed and is already proving to be a valuable asset. The cut quality is far superior to our old saw. This means we know when we’re building a new stand design, each part will fit together perfectly, saving us a lot of time. It also means we don’t need to cut certain materials by hand to get the perfect finish.
“The in-built extraction system is also a great feature. Dust around the saw is pretty much non-existent now thanks to the effective way the dust is taken off the blade during the cutting process. Not only does this make a cleaner environment for our workers, it also means we’re not having to spend much time cleaning the saw. These things may sound trivial but together, they make our business more efficient.”
John adds, “We’ve taken on four new carpenters in the last year to keep up with demand and as a result, the Striebig is already cutting considerably more sheets than its predecessor. In 2018, we were completing six to eight stands a month. In 2019, we were seeing those numbers being completed each week. Now, thanks to the introduction on new machinery like the Striebig Compact wall saw and continual investment in our team, we’re on target to complete 25 stands each month. Order numbers are really rocketing and it’s clearer than ever that good quality machinery is invaluable to us. We certainly couldn’t complete these kind of orders each week without our Striebig.”
For more information from TM Machinery Sales Ltd, call us on 0116 271 7155 or email sales@tmservices.co.uk. For the latest news, follow TM Machinery on Twitter: https://twitter.com/tm_machinery.
Issued by Catherine Earle, CSJ Public Relations. Tel: 07701 037 351. Email: catherine@csj-pr.co.uk